Controlled Bolting – Torque
Joint Integrity
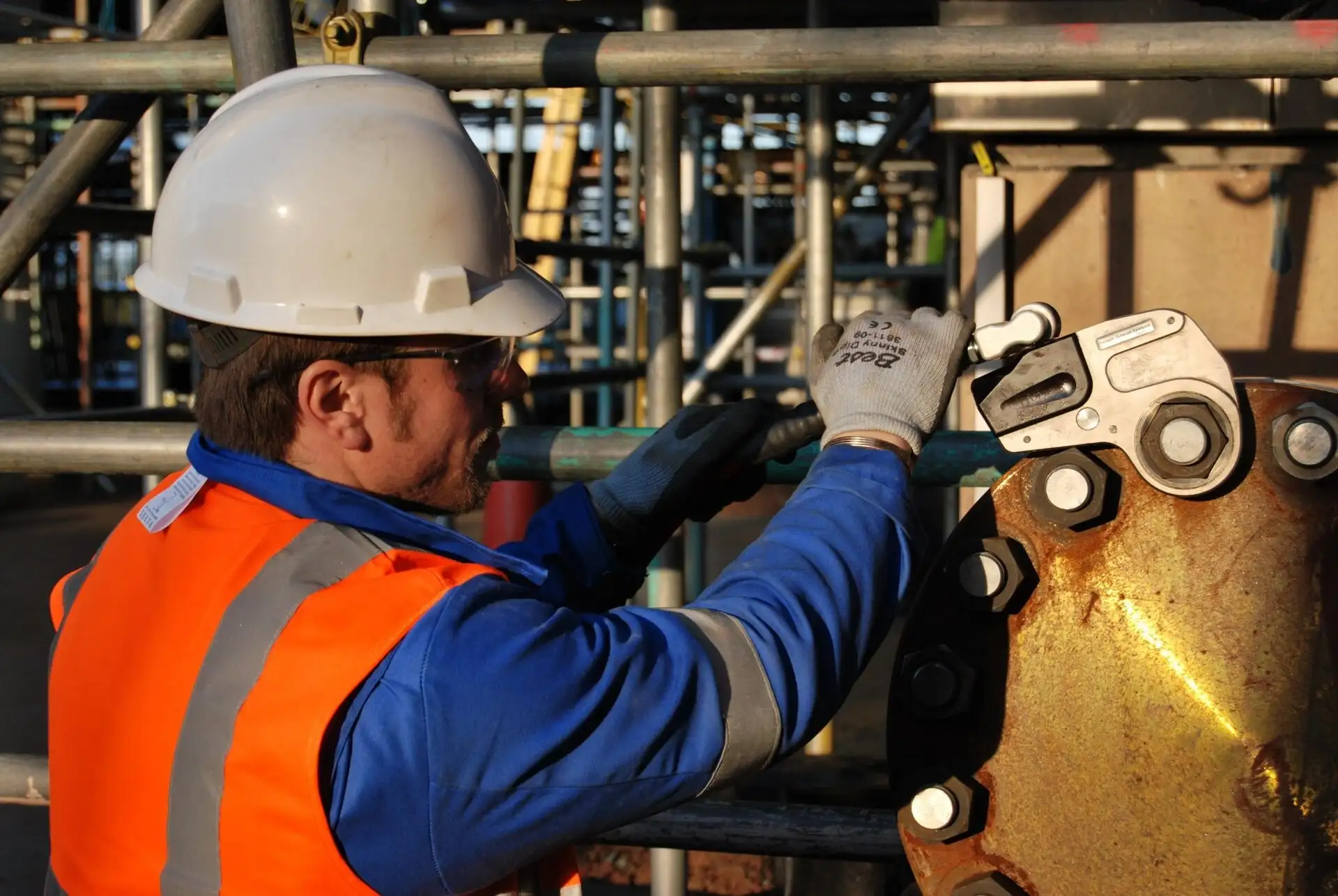
Our Joint Integrity division strive to exceed all our client’s expectations by delivering a leak free start up in a timely, safe manner.
The importance of planning the joint assembly, preparation of all components, procedures, tooling and ensuring application of the correct methodology is essential.
The principle of a bolted joint is based on the induced bolt load delivering sufficient joint compression and gasket seating stress to withstand maximum service pressure and forces. This is when the bolting is under tensile load. A minimum level of operational gasket seating stress must be maintained throughout joint service, therefore the design bolt load/compression target on installation should allow for creep, relaxation, uncertainty over service loadings and the tolerances of components and tools used.
This load can be applied by various different methods but there are certain constants that must always be in place to ensure a leak free joint.
Preparation – The sealing faces must be clean and free from serious damage. The bolting must be prepared correctly (lubrication if torquing, thread protrusion if bolt tensioning).
Equipment – Should be fit for purpose and have valid calibration certification.
Personnel – All personnel engaged in the tightening of bolted connections should be trained in the equipment being used and have the appropriate qualifications.
With our fully trained and highly motivated staff, quality tooling and procedures born out of experience, we aim to eliminate the worry associated with all of this.
Joint Integrity Standards
Our Joint Integrity division strive to not only meet but to exceed all our client’s expectations by delivering a leak free start up in a timely, safe manner.
Whether it is a single bolted connection or a multi-million-pound project, we approach each task with the same level of importance.
We believe with the correct preparation, using competent personnel, calibrated innovative equipment, proven methods of operation, propriety asset management software and bolt load calculations traceable to ASME PPC1 2019, that “All leaks are preventable”.
Our quality and safety records will stand up to any scrutiny, additionally supported by our extensive track record in this service.
The strength of any company is its employees and at WSG, all our joint integrity personnel are competent to Industry recognised ECITB TMJI Hand Torque and Hydraulic Torque standards. Bolting Technicians also have a CCNSG (Contractor Safety Passport) and relevant Offshore Survival & Medical certificates.
Proving competency to TMJI level should be the minimum standard and we both select and provide personnel who have experience and a wide range and understanding from many industries.
We recognise that different working environments provide different challenges whilst onsite. The necessary skills and experience required to break out a refinery reactor safely and on time vary from those required on a construction project.
We understand that personnel selection is a key factor to our success.
Our Locations
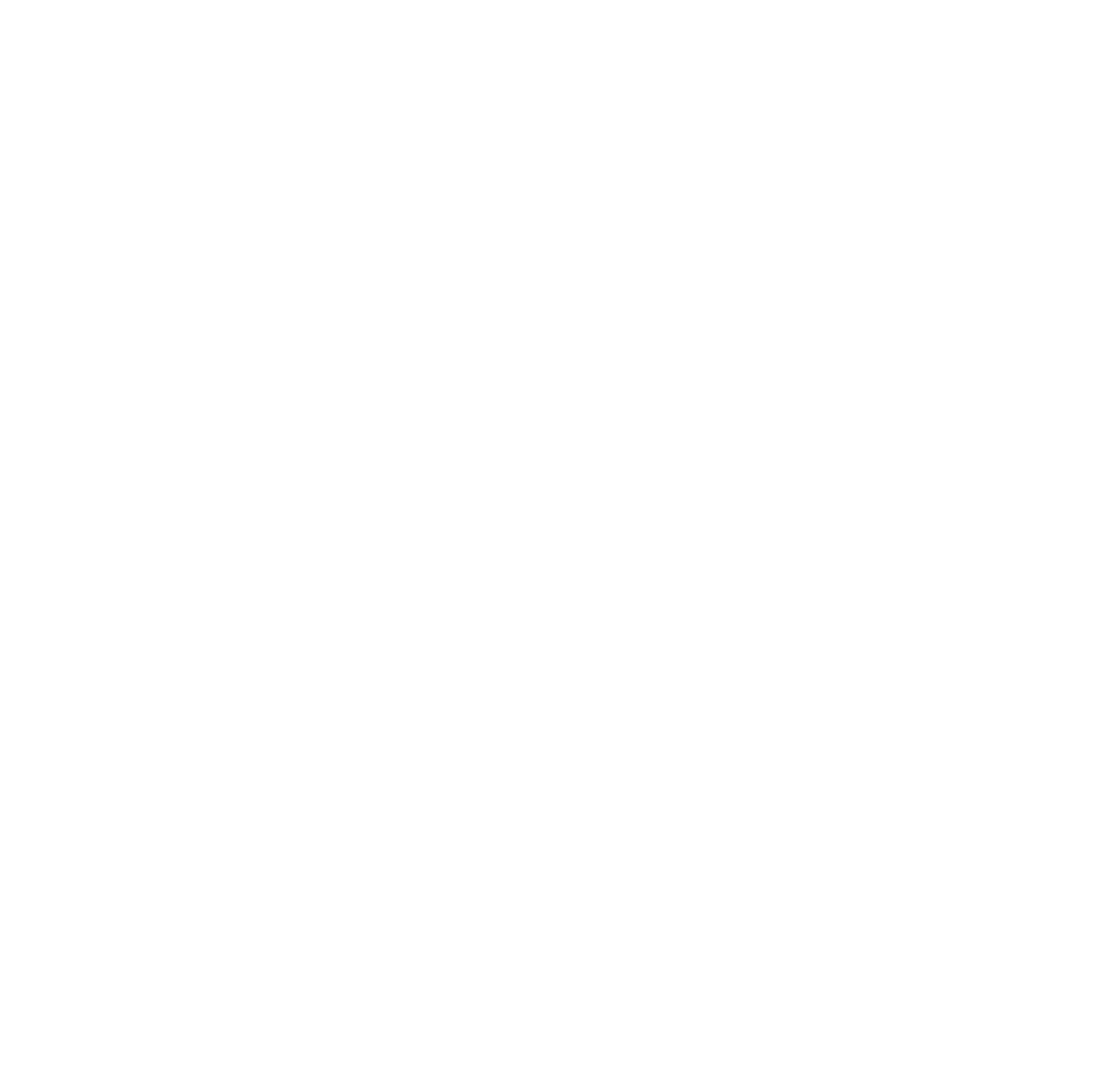